Any physical product part of the global supply chain spends most of its time stored in a warehouse. So, if any issues make the process less efficient, dealing with them must remain a priority. In light of that, here are the top five warehouse optimisation tips to keep things as smooth as possible. We’ll also observe how a warehouse management system helps you plan ahead with it.
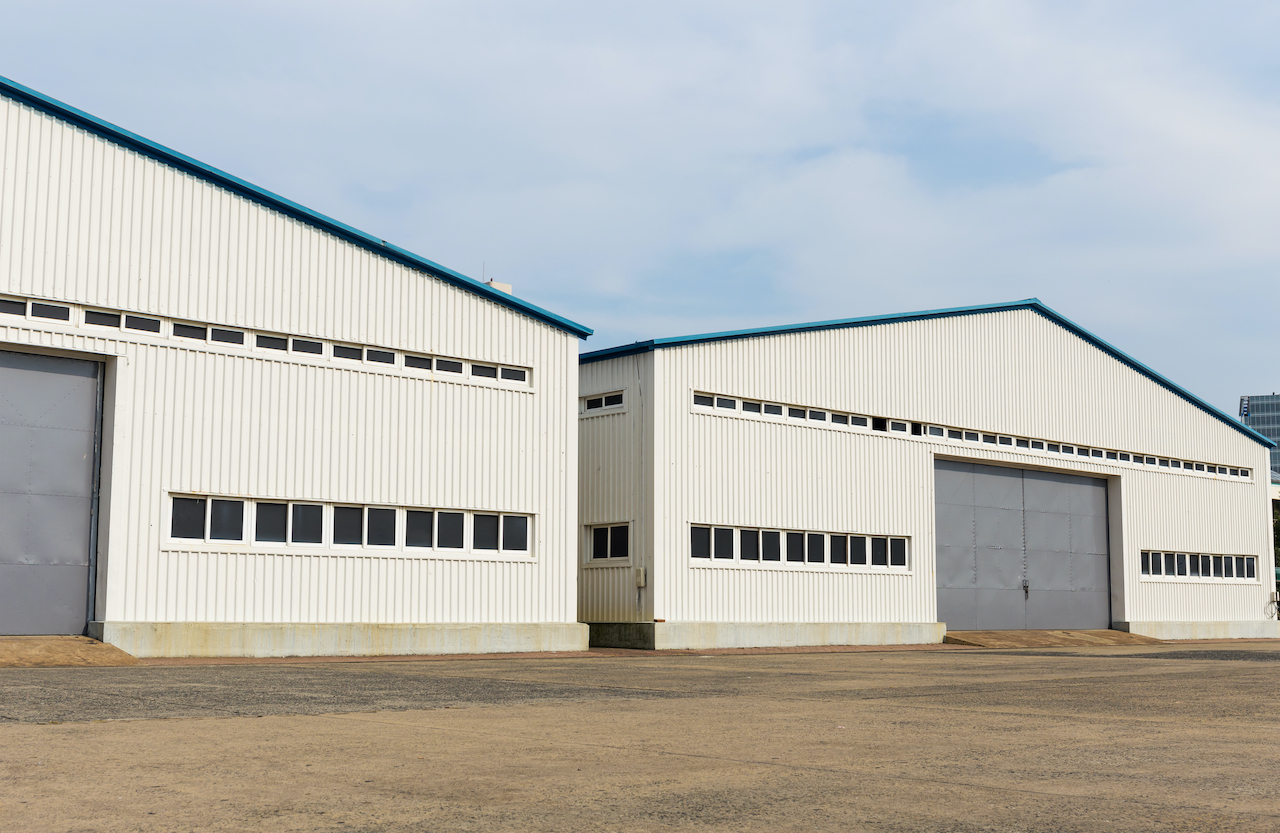
Why Warehouse Layouts Are Important for Managers
An optimised warehouse layout design makes storing or extracting packages more manageable and more straightforward for the managers to conduct regular inspections. With a digital warehouse management system, the process can even be automated. They can observe the reserved stock and monitor the status of all the employees within the premises.
Warehouse Layout Tips for Optimisation
Given the various benefits an excellent warehouse layout can bring, let’s look at the best tips you can implement to achieve it.
Choose the Ideal Design
Like all great inventions, the ideal product starts from the design stage. Thus, if you wish to make your warehouse efficient, you better start with the drawing board. Depending on the location, each warehouse can suit one of three configurations, and it’s your responsibility to choose the right one.
- U-Shaped: The most uncomplicated design you can go for, a U-shaped warehouse has a storage area in the centre, with two loading/unloading bays on either side. It is best to have one of those for arrivals and the other for taking out deliveries.
- I-Shaped: Also known as the follow-through design, it’s best for busy warehouses that need more space to accommodate parking. The travel length is longer, but it keeps the transit flowing with minimal interruptions.
- L-Shaped: When you have a facility that has limited access to the road or is in the process of being upgraded, having an L-shaped layout works wonders. It allows multiple avenues of incoming/outgoing vehicles and can help you make the most of a limited space.
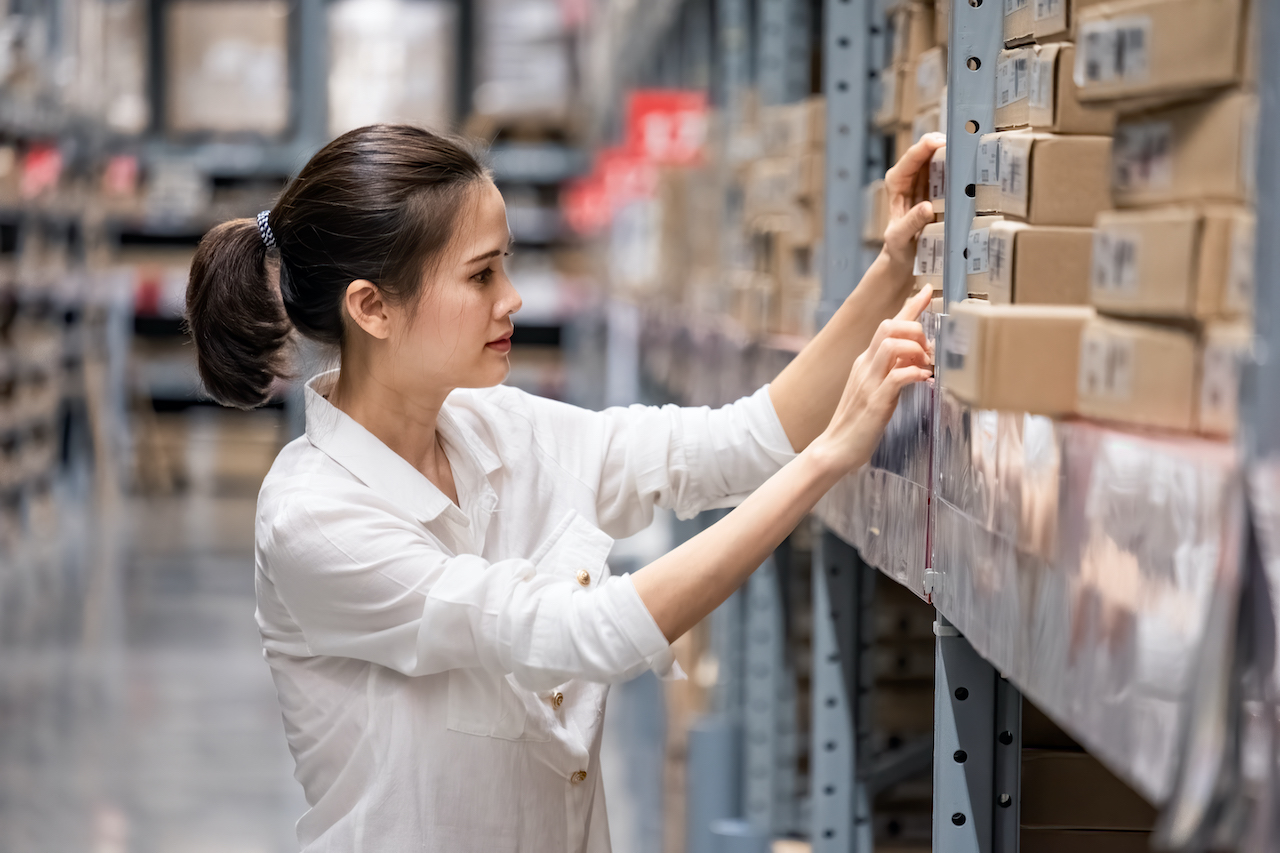
Plan For Space Optimisation
For a warehouse, every square inch of room counts toward the business’s bottom line. It can save the customers a minute less wait time and your suppliers a dollar for every shipment. You can add additional slots using the vertical space and designating compartments by package size.
Invest in Automated Equipment
The human body can only endure so much. So, if you desire to make the most of your staff, it’s best to augment them with specific automation equipment. It will take at least a few decades before we have something like Blade Runner, but you can install automated lifts and support drones to take some of the load off.
Install a Warehouse Management System (WMS)
In a digital age, it would be wise to utilise a system that keeps track of all packages. A multi-faceted warehouse management system can handle the pressure and let you know the inventory status in real time.
Prepare a Test Run
Regardless of what kind of systems you put in place, running a trial before taking things full-scale is always an excellent idea. That lets you realise the system’s true potential and iron out any glitches without extensive losses.
Concluding Thoughts
Operating a warehouse involves several complicated processes. It helps to trust a specialist with all the systems to keep things stable and, in turn, profitable. For Singapore’s best warehouse management systems, check out Qbasis for a free quote today.