Barcodes, a residual technology of the Cold War, have influenced several crucial sectors, from retail to logistics. Scanning a barcode can tell you all about the item, from its origins to the required conditions for storage.
While big corporations are financially content with creating a barcode inventory management system, small and medium businesses (SMBs) may face obstacles due to scale. Yet, the availability of that feature can bring several advantages to any enterprise. Here’s a short guide on how SMBs can have barcodes for their inventory system.
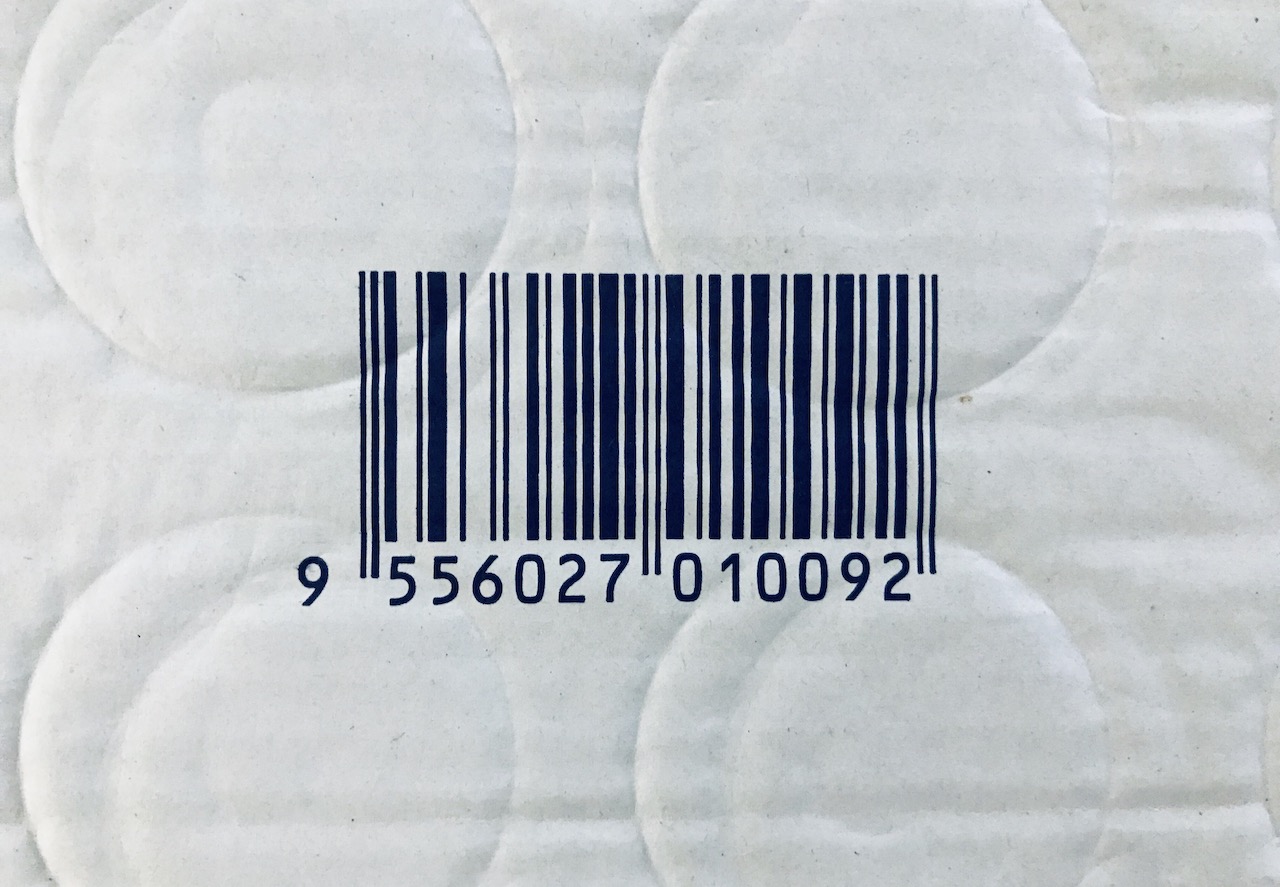
What Are Barcodes?
You can consider barcodes as a representation of several lines of data within a single picture. A few barcodes have attached numbers to ensure precise readings. A scanner converts that information to readable data within a fraction of a second. The numerals are for manual operation if the original code is no longer readable.
There are two kinds of barcodes currently in commercial use.
1-D Barcodes
It is the most popular form of barcode you can find. 1-D barcodes contain multiple lines of varying widths. The lines’ order and width let the barcode reader obtain the relevant input.
2-D Barcodes
2-D barcodes are scanned over an area instead of a line. They may take longer to scan but offer far more possible combinations and contain more information than 1-D barcodes. The most well-known examples are in the form of QR codes.
What To Consider With a Barcode Inventory System?
The barcode inventory system can create more efficient stock storage for every business. However, that efficiency can vary with scale and industry type. So, it’s best to consider a few influential criteria before deciding on the best approach for your business.
Inventory Goals
Before deciding on the system, it helps to set your inventory goals. Measure the available space and other storage factors to determine which barcode system might suit you best. You want to spend only a few resources for short-term storage or limited stock.
Software
The efficiency of your barcode system is only as good as the software for keeping track of the inventory. It’s best to avail of something that can run on all the computers within your organisation. At Qbasis, we can deliver a customised solution that can relay the information on smartphones or through RFID chips for easier access.
Hardware
Any software is only as good as the hardware supporting it. Therefore, you must collect a good barcode generator and scanner compatible with your system. The labels must remain visible until the packaging gets discarded.
It is best to prefer a company that caters to software and hardware requirements. Qbasis is one such enterprise that you can count on.
What Are the Steps in Implementing a Barcode Inventory System?
If you desire to implement barcodes in your inventory system, you must follow a prerequisite procedure mentioned below.
Study and recognise industry barcode standards
There are several standards for applying the optimal barcode system for specific situations. Instead of building one from the ground up, you can avail of those presets from an external contractor. Sure, there can be a few edits that make it more suitable for your application, but the overall structure remains primarily unchanged.
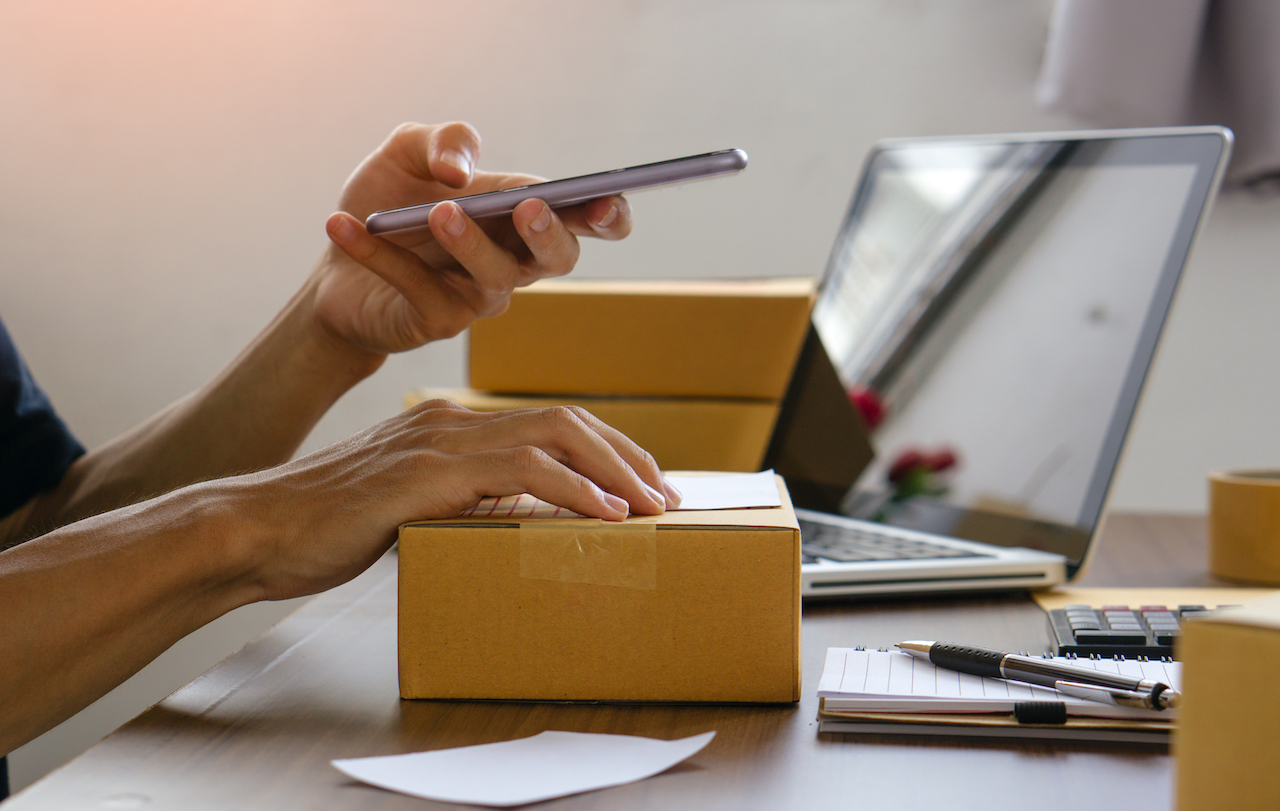
Identify barcode functions
Determine the scope of asset management that you’re trying to enhance. It is the part where you choose from an SKU (Stock Keeping Unit) or UPC (Universal Product Code). The former can help you configure the current stock in the inventory. With the latter, you can use the same code throughout the supply chain, even with variations in packaging.
Provide the information to store in the barcodes
You can stock your warehouse smartly if you and your employees have the relevant information from the barcode. The barcodes can provide any or all of the following information from each scan.
- Item name and description
- Variations such as size, weight, or colour
- Product category
- Purchase cost
- Vendor information
- Store/warehouse location
It’s also wise to consider the location of the barcode scanner. Depending upon the supply, you want one close to the loading bay or the exit.
Select software and hardware
After knowing all the prospects, it’s time to choose the adequate tools to make it a reality. An automated inventory management system needs suitable software and hardware. So, choose the one compatible with the barcodes you desire to apply.
It helps to choose the barcode reader, label printers, charging stations, cables and other equipment within the predicted budget. In addition, it helps to take into account the downtime for installation so that you can plan your operations ahead of time.
Implement barcode inventory procedures
Now, you can integrate the barcodes into your inventory management system. Choose the most suitable stock for the transition and apply the necessary changes. This stage also includes training the staff in the barcode scanner usage and the putaway procedure changes. You may need to reconfigure the sorting system as well.
Summarising
Equipping your inventory management system with barcodes can cause any SMB to grow substantially. We hope this guide assists in choosing the best configuration as per your requirements. For more information or further reading on warehouse or energy management systems, connect with Qbasis today.